LEED v4 Benefits for Precast Concrete Manufacturers
- < Product Manufacturers Take Notice of Perkins + Will’s Precautionary List
- > How the New PCR Program May Affect Your LEED v4 EPD
How do precast concrete products fit into the LEED v4 rating system? What LEED credits apply to precast concrete products? The National Precast Concrete Association (NPCA) has released The Precaster’s Guide to LEED v4 to help manufacturers navigate the LEED rating system. Over the past couple of years, precast concrete manufacturers have helped project teams contribute points to several LEED projects. Let’s explore how precast concrete products can contribute to LEED v4.
LEED for Neighborhood Development Location Credit
The intent of this LEED credit is “to avoid development on inappropriate sites. To reduce vehicles miles traveled. To enhance livability and improve human health by encouraging daily physical activity.” Neighborhoods following the program must include a range of sustainability features, such as walkability, transit access, sensitive land protection, connectivity and shared infrastructure. To meet this credit, the project must be located within the boundary of a LEED-certified Neighborhood Development. The NPCA states that precast concrete products can help contribute points for this LEED credit because precast concrete-
• is ideal for compact multi-story construction projects
• arrives to the construction site ready to be installed
• contributes to a reduced footprint for sensitive land
• can be used for shared infrastructure such as storm water treatment
• improves energy efficiency with thermal mass qualities
• can contribute to heat island reduction through highly reflective surfaces
Sustainable Sites LEED v4 Credits
There are many opportunities for precast concrete manufacturers in the Sustainable Sites LEED category . The Sustainable Sites category rewards decisions about the environment surrounding the building, with LEED credits that emphasize the relationships among buildings, ecosystems, and ecosystem services. Sustainable Sites focuses on restoring project site elements, integrating the site with local and regional ecosystems, and preserving the biodiversity that natural systems rely on. Let’s review how precast concrete manufacturers can benefit from these LEED credits.
Site Development – Protect or Restore Habitat:
The intent of this LEED credit is “to conserve existing natural areas and restore damaged areas to provide habitat and promote biodiversity.” This credit is achieved by using native or adapted vegetation, restoring 30% (including the building footprint) of all portions of the site identified as previously developed with native or adapted vegetation.
The NPCA recommends the following strategies. A multi- story building with a vegetated roof is a great candidate for precast concrete construction. Another potential strategy for increasing density is to locate parking areas within the building footprint to limit site disturbance. A parking garage – often built with precast/pre-stressed concrete – can be located within a building to help maintain adjoining natural areas that would otherwise be consumed by surface parking.
Open Space LEED Credit:
The intent of this credit is “to create exterior open space that encourages interaction with the environment, social interaction, passive recreation, and physical activities. For this credit, the project must provide an outdoor space greater than or equal to 30% of the total site area (including the building footprint). A minimum of 25% of that outdoor space must be vegetated or have an overhead vegetated canopy. Precast concrete multi-story buildings are well suited to support vegetated roofs.
Rainwater Management LEED Credit:
The intent of this credit is to “to reduce runoff volume and improve water quality by replicating the natural hydrology and water balance of the site, based on historical conditions and undeveloped ecosystems in the region.” The NPCA notes that precast concrete systems such as filtration planters or bioretention cells mimic natural hydrology by in infiltrating runoff water into the groundwater or enabling it to evaporate into the atmosphere.
Through a variety of physical, biological and chemical processes, pollutants are removed from the storm water before returning to underground aquifers or surface waters. The planters act as temporary storage for runoff water, helping minimize discharge rates. To learn more about this new LEED v4 credit please refer to the video education course Don’t Get Soaked: Smart Strategies to Manage Rainwater .
Heat Island Reduction LEED Credit:
The intent of this credit is “To minimize effects on microclimates and human and wildlife habitats by reducing heat islands.” Option 1 encourages the use of site shading and reflective pavements and roofing materials or vegetative roofs. Option 2 encourages underground or shaded parking areas. The NPCA notes that light-colored surfaces have a high SR. Conventional grey concrete generally has an initial SR of greater than 0.35. Concrete made with white cement can have an SR greater than 0.70.
Energy and Atmosphere LEED v4 Credits
The Energy and Atmosphere LEED category approaches energy from a holistic perspective, addressing energy use reduction, energy-efficient design strategies, and renewable energy sources. There are two primary LEED credits in this category that may benefit precast concrete manufacturers.
Minimum Energy Performance LEED Credit:
The intent of this LEED credit is “to reduce the environmental and economic harms of excessive energy usage by achieving a minimum level of energy efficiency for the building and its systems.”
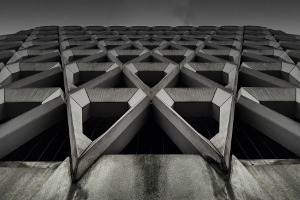
Optimize Energy Performance LEED Credit:
The intent of this LEED credit is “to achieve high levels of energy performance beyond the prerequisite standard. This includes establishing an energy performance target in early design phases.”
The NPCA recognizes many benefits for precast concrete manufacturers regarding the two LEED credits. Buildings constructed with precast concrete can achieve high levels of energy efficiency. Precast concrete has high thermal mass because a lot of heat energy is required to change its temperature. With its high thermal mass, precast concrete acts like a thermal sponge, absorbing heat during the summer to keep the building’s interior cool and storing heat from the sun that is released slowly at night when temperatures fall.
Materials and Resources LEED v4 Credits
The Materials and Resources credit category focuses on minimizing the embodied energy and other impacts associated with the extraction, processing, transport, maintenance, and disposal of building materials. The requirements are designed to support a life-cycle approach that improves performance and promotes resource efficiency. Each requirement identifies a specific action that fits into the larger context of a life-cycle approach to embodied impact reduction. We will review the major LEED credits that precast concrete manufacturers can contribute to.
Building Life-Cycle Impact Reduction LEED Credit:
The intent of this credit is “to encourage adaptive reuse and optimize the environmental performance of products and materials.” The LEED credit offers several options for reducing the impact of buildings, mostly focused on existing building adaptation and reuse. However, for new buildings, Option 4 encourages the use of life cycle assessment to demonstrate lower environmental impact of the proposed building by 10% over a baseline building.
The NPCA states that precast concrete structures are known for durability and long service life, resulting in a reduction of the environmental impacts associated with reconstruction, repair and maintenance. Precast structures demonstrate low life cycle impacts. A precast concrete life cycle assessment is available at www.precast.org and can be used in the pursuit of this credit.
Building Product Disclosure and Optimization – Environmental Product Declaration LEED Credit:
The intent of this credit is to “encourage the use of products and materials for which life-cycle information is available and that have environmentally, economically, and socially preferable life-cycle impacts. To reward project teams for selecting products from manufacturers who have verified improved environmental life-cycle impacts.” Precast concrete environmental impacts – when compared with many other materials – will compare favorably as a primary building and infrastructure material.
Building Product Disclosure and Optimization – Sourcing of Raw Materials LEED Credit:
The intent of this credit is “to encourage the use of products and materials that have life cycle information and have environmentally, economically and socially preferred life cycle impacts.” The NPCA states that precast concrete can help contribute to recycled content since most structures contain recycled material such as y ash, slag and reinforcing. Fly ash and slag would be considered pre-consumer recycled content while reinforcing steel is mostly post-consumer.
Building Product Disclosure and Optimization – Material Ingredients LEED Credit:
The intent of this credit is to reward project teams for selecting products for which the chemical ingredients are inventoried using an accepted methodology and for selecting products that minimize the use and generation of harmful substances. Precast concrete manufacturers can meet the requirements for this credit by developing a LEED v4 compliant HPD. Additional resources on HPD development can be found at Elixir Environmental .
Indoor Environmental Quality LEED v4 Credits
This LEED category rewards decisions made by project teams about indoor air quality and thermal, visual, and acoustic comfort. Green buildings with good indoor environmental quality protect the health and comfort of building occupants. High-quality indoor environments also enhance productivity, decrease absenteeism, improve the building’s value, and reduce liability for building designers and owners.
Low-Emitting Materials LEED Credit:
The intent of this credit is to reduce concentrations of chemical contaminants that can damage air quality, human health, productivity and the environment. According to the NPCA, exposed precast concrete is an excellent choice for finish material, eliminating the need for additional material to be applied on the interior. Precast concrete is defined as an “inherently non-emitting source” of VOCs in LEED v4 and therefore can demonstrate compliance to this credit without any VOC emissions testing.
Daylight and Quality Views LEED Credit:
The intent of these credits is to provide for the building occupants a connection between indoor spaces and the outdoors through the introduction of daylight and views into the regularly occupied areas of the building. The NPCA states that precast concrete floor systems can span large distances with shallow floor plates and column- free spaces to help achieve these credits. Precast concrete can also be exposed on ceilings to reflect light deep into interior spaces.
Acoustic Performance LEED Credit:
The intent of this credit is to provide workspaces and classrooms that promote occupants’ well-being, productivity and communication through effective acoustic design. Precast concrete offers excellent noise control in two ways. First, precast concrete floors and walls effectively block airborne sound transmission over a wide range of frequencies. Second, precast concrete effectively absorbs noise, thereby diminishing noise intensity. This means that precast concrete can demonstrate compliance to this credit either through calculation or measurement.
In conclusion, there are several opportunities for precast concrete manufacturers to contribute to LEED v4 projects. Has your company helped project teams any of the LEED credits we discussed today?
For more information or to discuss the topic of this blog, please contact Brad Blank